Asphalt mixing plant is also called asphalt concrete mixing plant, asphalt concrete plant, and asphalt mixing equipment.
Asphalt batch mixing plant refers to a complete set of equipment for mass production of asphalt concrete, mainly composed of cold aggregate supply system, drying drum system, mixing building, filler storage and supply system, asphalt supply system, mixing system, asphalt mixture storage silo, Pneumatic system, filtration system, control system, environmental protection system, etc.
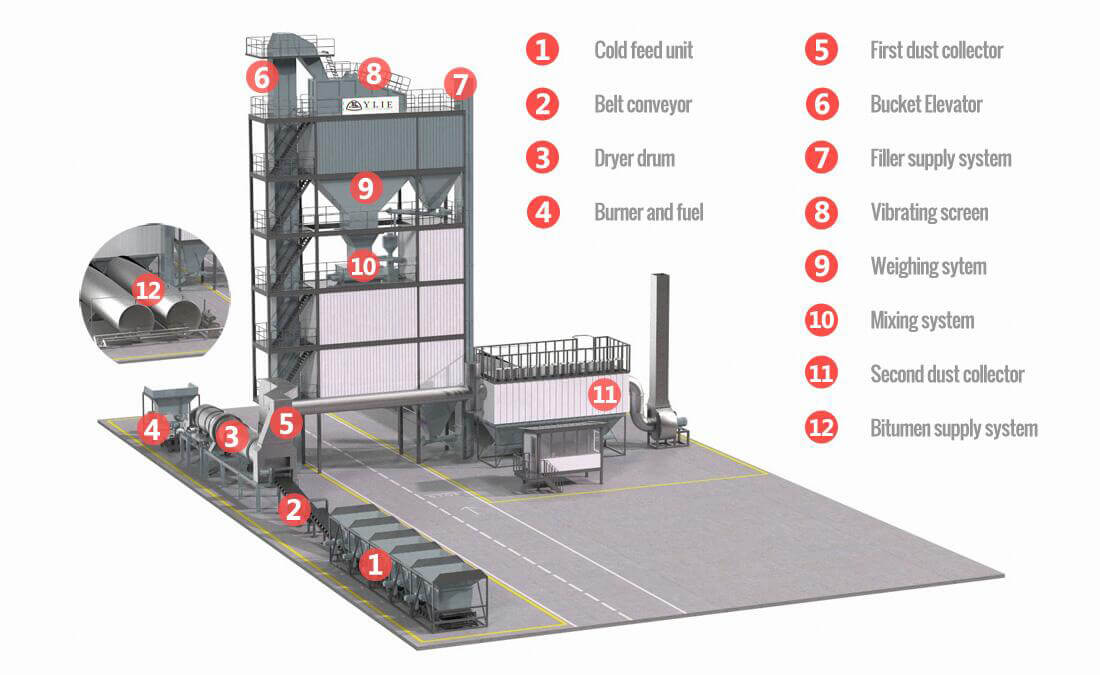
The intermittent asphalt hot mix plant has the advantages of large output, precise proportioning, uniform mixing, stable operation, and fixed site. It is widely used in road construction such as highways, ports, airports, national roads, water conservancy, and bridges. The equipment can produce asphalt mixture, modified asphalt mixture, colored asphalt mixture, fully meet the different engineering needs of customers.
Batch type means that the heating and drying of the aggregate and the stirring of the mixture are forced to be carried out periodically. The equipment stirs one pot and one pot separately, and each pot is stirred for 45 seconds to 60 seconds, and the output depends on the model of the equipment.
Work flow of standard asphalt batch mixing plant
1. Filter from different cold aggregate silos to conveyor.
2. The conveyor supplies cold aggregate to the drying drum.
3. Drying drum with burner to heat cold aggregate.
4. The aggregate elevator sends the hot aggregate to the vibrating screen.
5. The vibrating screen divides the hot aggregate into different silos according to size.
6. Aggregate scale weighs hot aggregate according to correct proportions.
7. The powder scale correctly weighs the powder in the powder extractor.
8. Asphalt scale correctly weighs asphalt.
9. Send the hot aggregate and powder to the mixer for even mixing, and spray asphalt while mixing.
10. Stir evenly and send to finished product silo or transport truck.
11. The process is controlled by the control system during this process.
12. According to environmental protection requirements, a dust removal system is optional to filter exhaust gas waste.
System Introduction
1. Sieving System
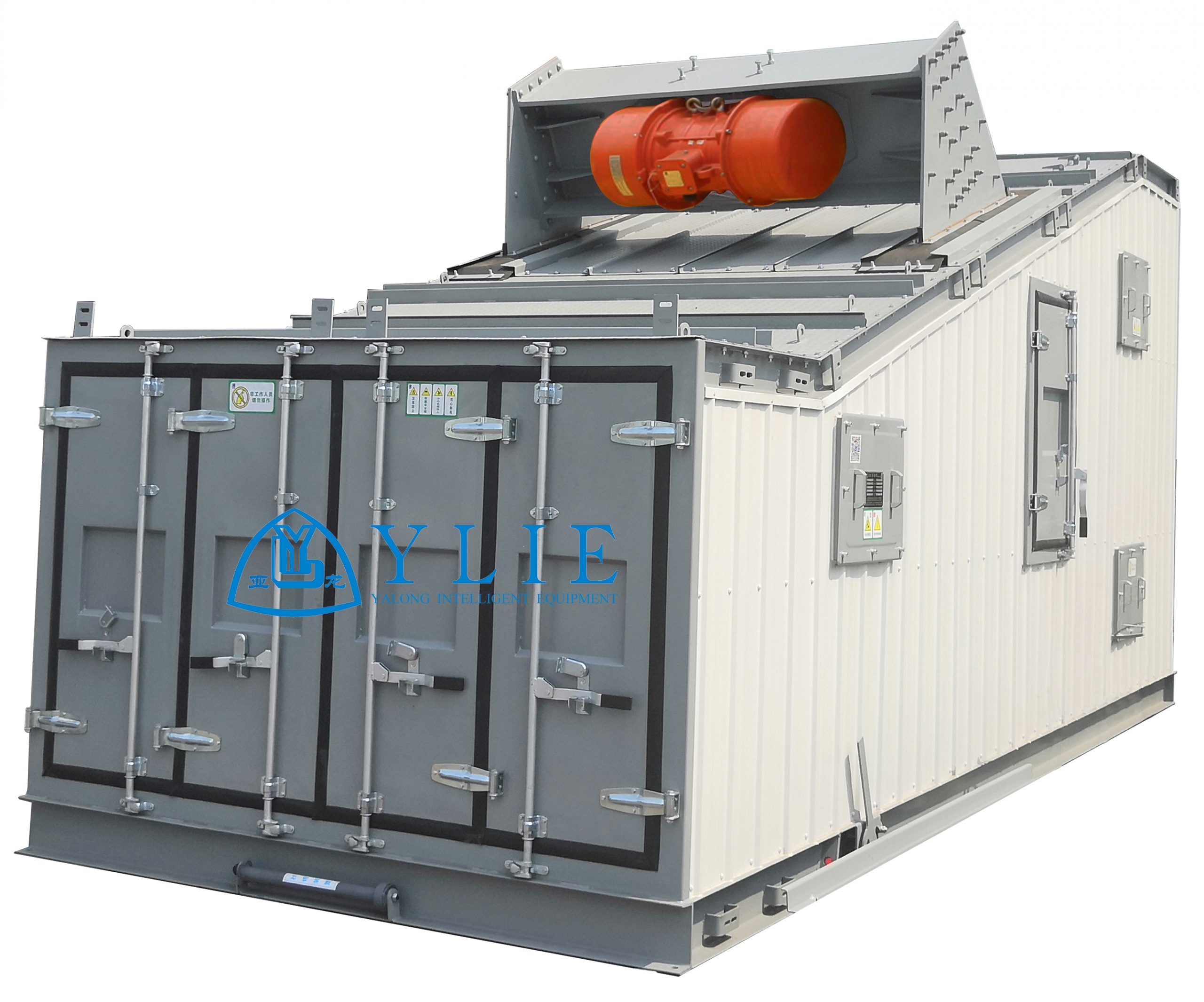 |
·The screening system is fully sealed to prevent impurities from entering the hot aggregate;
·Independently develop screening systems to improve screening efficiency and accuracy;
·The hot aggregate bin is separated by high-strength wear-resistant plates to avoid mixing of hot aggregates;
·Optional overflow waste treatment device to avoid affecting the screening of hot aggregates; |
2. Precision Metering System
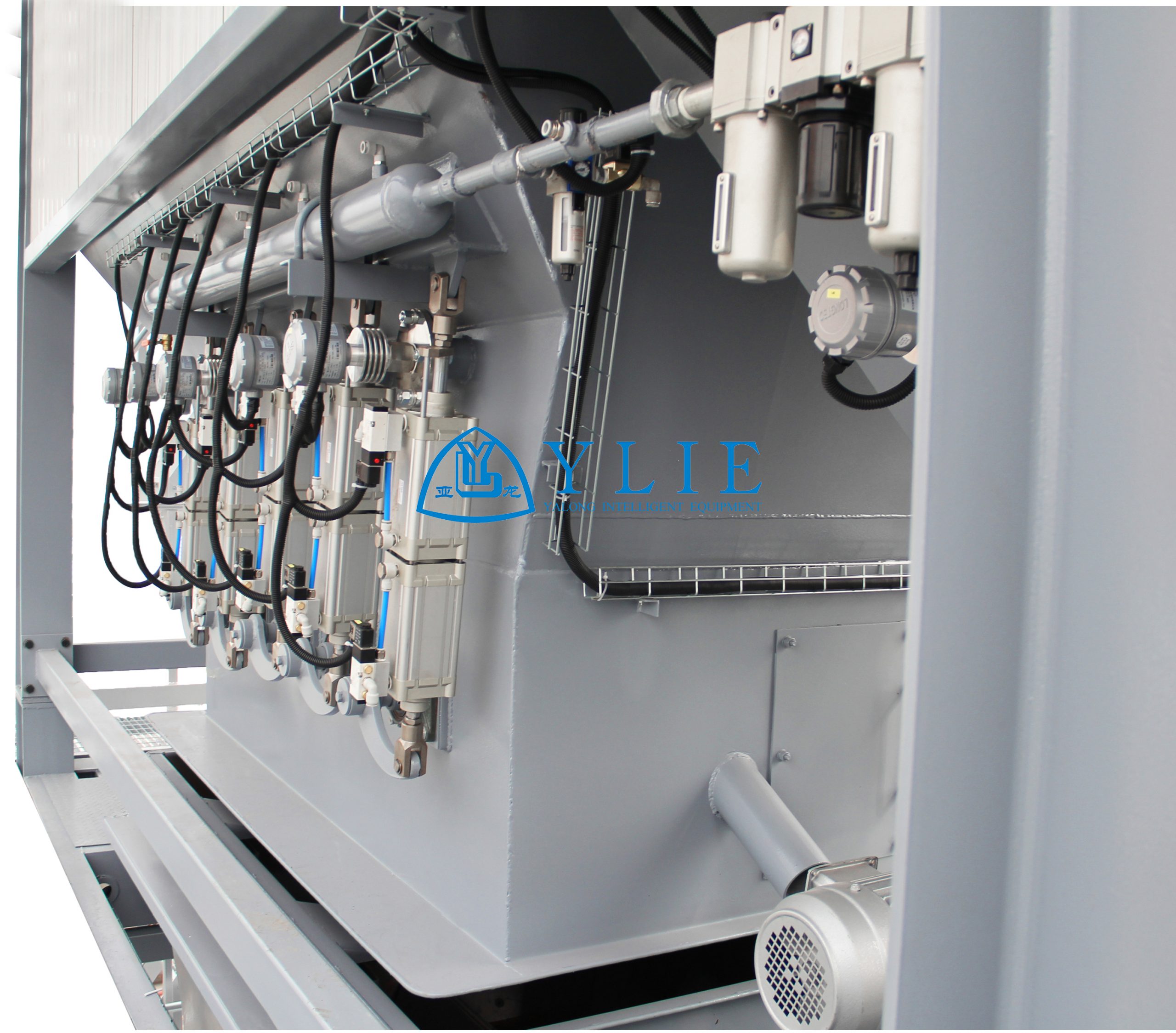 |
·Equipped with aggregate scale, filler scale, and asphalt scale, with automatic drop compensation, overweight alarm, and locking functions;
·The asphalt measurement adopts the dynamic measurement technology of secondary replenishment, and the drop is automatically corrected to achieve the accuracy of asphalt measurement: static ± 0.20%, dynamic ± 1.0%;
·The filling material adopts a non-equidistant measuring dedicated screw conveyor, which achieves a measurement accuracy of static ± 0.20% and dynamic ± 1.0%;
·The measurement of aggregates adopts dynamic flashing technology, with automatic correction of drop, which is fast first and then slow, to achieve measurement accuracy of static ± 0.3% and dynamic ± 2.0%; |
3. Stirring system
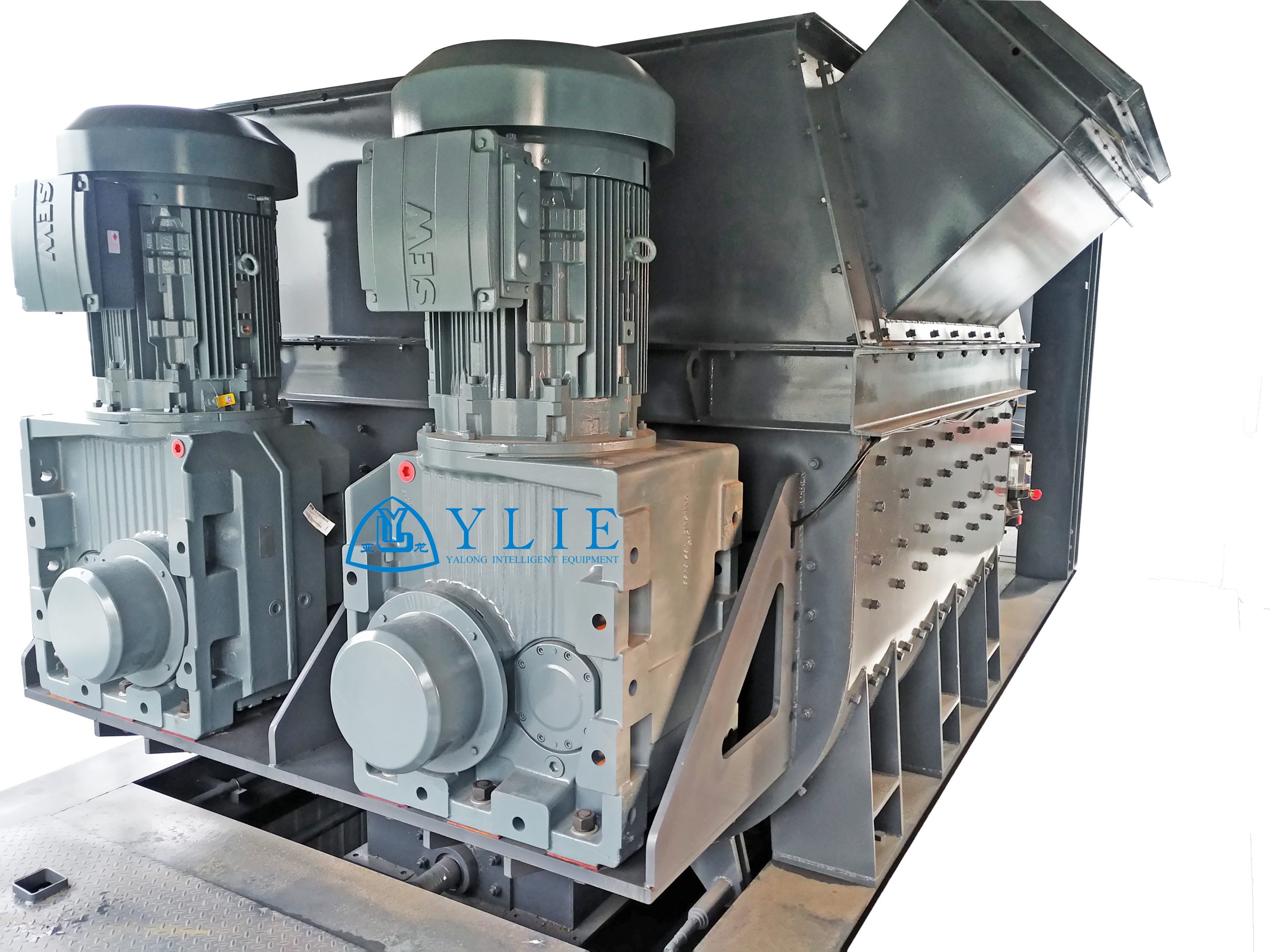 |
·The mixer designed and manufactured according to European standards has exceeded the standards in terms of service life, overload capacity, and other indicators.
·Two bevel gear reduction motors are independently driven, with synchronized gears for smoother operation;
·The mixing blades are made of high-strength wear-resistant alloy materials, with a working life of over 100000 batches.
·Reasonable mixing blade layout ensures more thorough and even mixing;
·High pressure asphalt spraying pump, shorter mixing time; |
4. Bitumen supply system
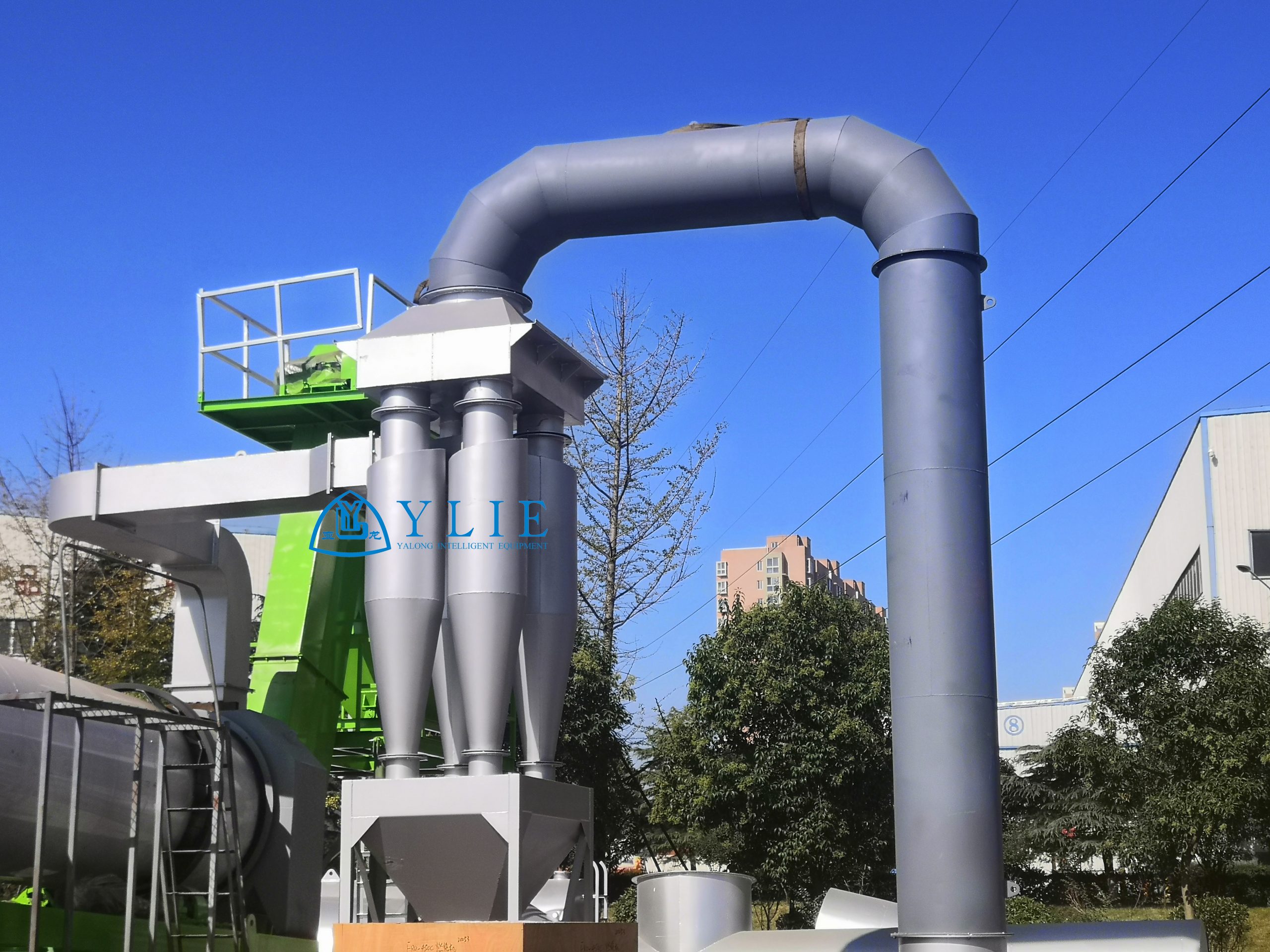 |
· Composition: asphalt tank, integrated light oil-burning and heat-conducting oil furnace (including pipeline and control cabinet), asphalt unloading tank (including screw-type asphalt pump), diesel tank.
·The asphalt tank adopts the modular concept design, which can be quickly installed and connected on site.
·High-performance thermal insulation design saves energy. All pipelines are thermally insulated with heat-conducting oil throughout the entire process. The asphalt tank is wrapped with 50mm rock wool for thermal insulation. It is equipped with ladders, platforms, inspection holes, continuous liquid level indicators and temperature displays.
· The internal serpentine tube layout is reasonable, and the heating speed is fast. |
5. Electronic control system
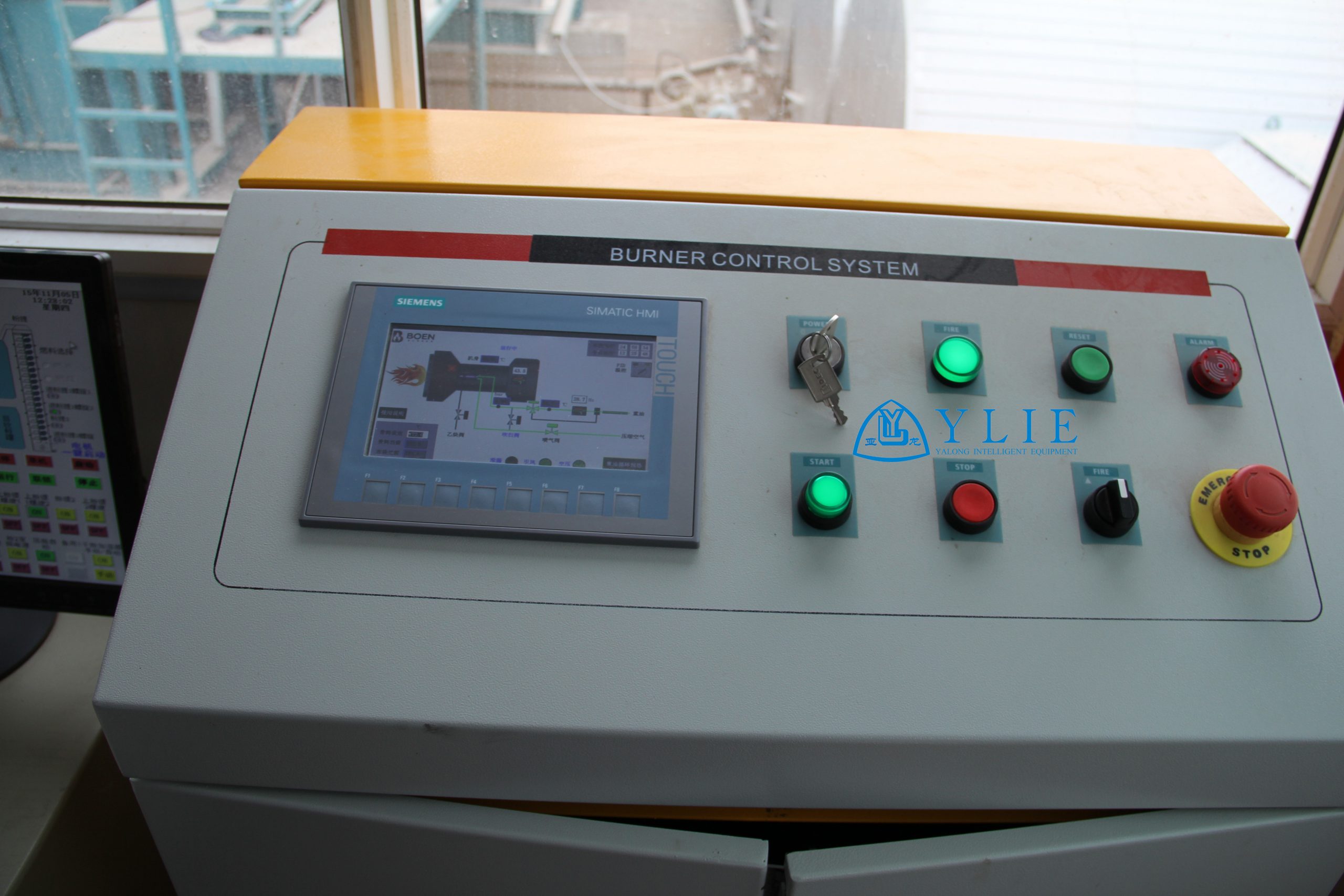 |
·The control components mainly use products from companies such as Schneider, Omron, and Mitsubishi;
·Using advanced foreign microcontrol technology, PLC, PC computer control equipment for operation;
·The central control room has sound insulation, heat insulation, moisture-proof, and dustproof sealing functions, and is equipped with a dual temperature cabinet air conditioning system for both cold and warm temperatures;
·All operations are centralized in one room, with automatic and semi-automatic control for easy operation;
·Fully automated with various printing modes such as synchronous tracking and historical statistical report
functions; |